Industrial electric motor systems
Most of the electricity used in the industrial sector is for motor-driven systems, making them one of the largest electricity consuming end uses globally. Electricity costs account for more than 90% of the total lifetime cost of ownership for a typical industrial electric motor. The number of motors in use will continue to grow while low-efficiency motors still represent two-thirds of the current stock. Improving the efficiency of motors and motor driven systems therefore plays an important role in reducing ownership costs and slowing electricity demand growth.
By doubling the energy efficiency of new industrial electric motor systems from 2022, SEAD member countries could deliver emission reductions of more than 800 MtCO2 in 2030. Doubling the efficiency of new industrial motor systems worldwide could reduce CO2 emissions in 2030 by more than a gigatonne, which is more than Japan’s energy-related CO2 emissions today.
The level of efficiency in a given industrial electric motor system will depend on both the extent to which efficient technologies are used and the design of the overall system. In most cases, improving the efficiency of a motor system includes the following actions:
- Using energy efficient motors;
- Selecting highly efficient core components (e.g. pumps, fans, compressors, transmission systems and variable speed drives) of the right type and size;
- Optimising the design and operation of the complete system;
- Periodic maintenance, timely replacement & retrofitting of controls.
Current policy coverage in standards and labels
International Efficiency (IE) standards stipulate the energy efficiency of low-voltage AC motors. Governments often use IE standards to specify the efficiency levels for their minimum energy performance standards (MEPS), as well as other policy measures. IE standards have five distinct levels. Motors categorised as IE1 or IE2 are comparatively inefficient. Those categorised as IE3 achieve roughly 96% efficiency. IE4 standard energy losses are about 15% lower than those from IE3 motors, and the more recent IE5 “ultra-premium efficiency” motor represents the highest level of efficiency that has been met by any current design.
As of late 2021, 57 countries have implemented MEPS for industrial electric motors, covering more than 40% of the global energy consumption of industrial motors, up from 15% ten years ago. Ukraine is the most recent country to introduce standards, which came into effect in 2021. Most governments only regulate new motors, but Pakistan also introduced MEPS and labels for refurbished second hand motors in 2021. Starting as a voluntary programme, it will eventually transition to compulsory registration and IE3 minimum performance requirements in 2023. Additional MEPS are expected to come into force in the Eurasian Economic Union countries in 2022. Currently, only 11 countries make use of mandatory comparative labels to incentivise sales for more efficient industrial motors, but eight additional countries offer voluntary comparative or endorsement labelling. Various countries have recently strengthened standards and extended scope. In China, Colombia and countries applying EU rules, for example, new motors on sale in selected product categories were required to meet at least the IE3 efficiency level from mid-2021. From 2023 onwards, some motor types have to meet the IE4 Super Premium requirements in the EU and other countries that apply EU rules.
This approach of relying on internationally harmonised efficiency levels is unique to industrial electric motors and provides many benefits for manufacturers and industrial facilities. It is the basis for the energy performance ladder approach.
The Energy Performance Ladder
In order to create large and growing markets for efficient appliances, the SEAD Initiative developed the Energy Performance Ladder that brings together multiple policies under a single consistent set of performance thresholds. These Ladder ‘steps’ are defined as energy performance levels using a standard test procedure. Governments can then set policy thresholds (such as MEPS, labels and high energy performance standards or HEPS) at different steps, as well as years in which the thresholds will move up the ladder.
The Ladder then provides a framework that can:
- Show a clear trajectory for improving appliance energy performance over time, by defining how policy will move up the ladder in future
- Benchmark energy performance across markets, while allowing policy to be set that is suitable for local market condition
- Aggregate markets to reduce costs and make highly efficient products more widely available.
An illustration of the Energy Performance Ladder with current and planned MEPS levels for industrial electric motors is depicted below.
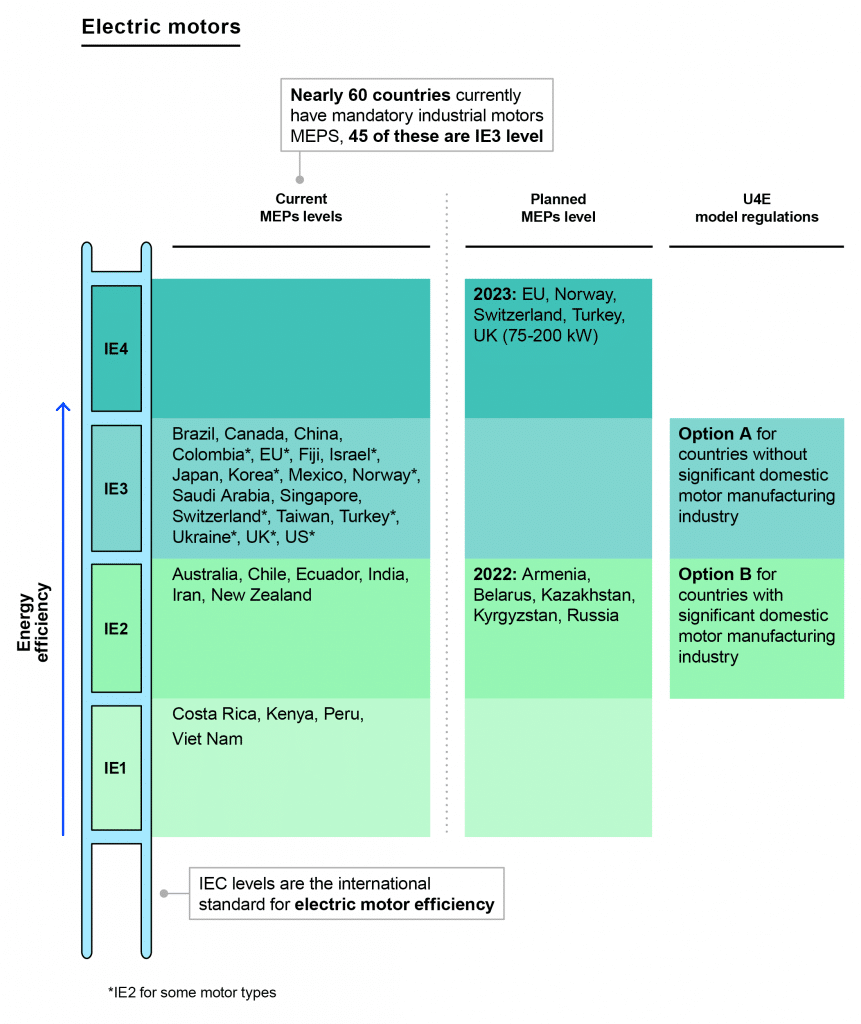
Of the 57 countries that currently have mandatory industrial motors MEPS, 45 of these are at the IE3 level. The European Union, Norway, Switzerland, Turkey and the United Kingdom are transitioning to IE4 levels in 2023 for motors in the 75-200 kW range. Large–scale additional energy savings will be available through early replacement of motors, variable speed drives, improved controls and system optimisation.